6. 12. 2024
Removal of metals (5 cm wires) from pulp in the production of paper towels (case study)
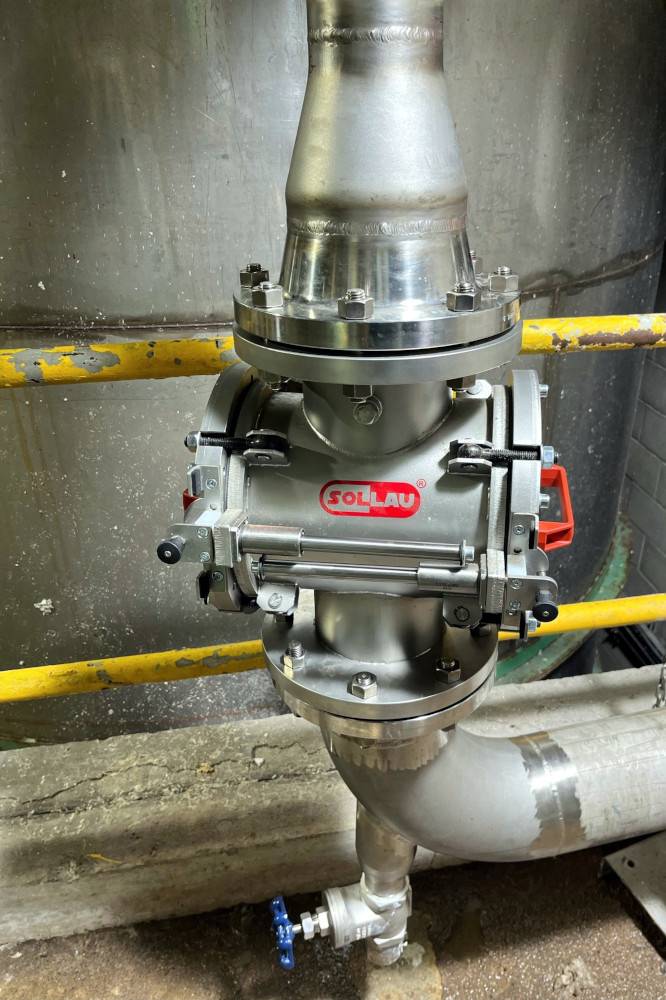
Initial status
Our customer is a leading manufacturer of high-quality paper products, including toilet paper, paper towels and tissues.
Problem
There are ferrous contaminants in the pulp. The pulp density is in the range of 2 – 5 %. The pulp is conveyed through a pipe with a diameter of 150 mm. The pipeline pressure varies between 1.4 and 4.1 bar.
Ferromagnetic particles not only threaten to damage the production technology but also adversely affect the final product quality.
Solution
Crushed pulp (cellulose) is a material that is difficult to treat by magnetic separation, as it can quickly clog conventional magnetic separators. Therefore, we chose the place where the pulp is transported by pipeline (DN 150). Our recommendation was to apply the inline plate magnet ML-P 150 N with strong neodymium magnets.
This separator design allows the free material flow because the very strong magnets are located on the doors. And as the doors move on slides, the separator cleaning is quick and safe.
After separator installation we could reliably catch the iron wires. Their length was most often around 5 cm.
Benefits of using the ML-P 150 N inline plate magnet
The risk of ferrous particles getting into the final products has been completely eliminated. It has contributed to the increased quality and customer satisfaction.
Applied equipment: ML-P 150 N inline pneumatic plate magnet
Benefits of the ML-P 150 N Inline Pneumatic Plate Magnet
- high pull-off force
- durable stainless steel design
- pressure resistance up to 10 bars
- suitable also for materials of worse pouring properties
- manual cleaning
- vertical and horizontal application