25. 4. 2025
Maximum purity coolant for precision honing and drilling (case Study)
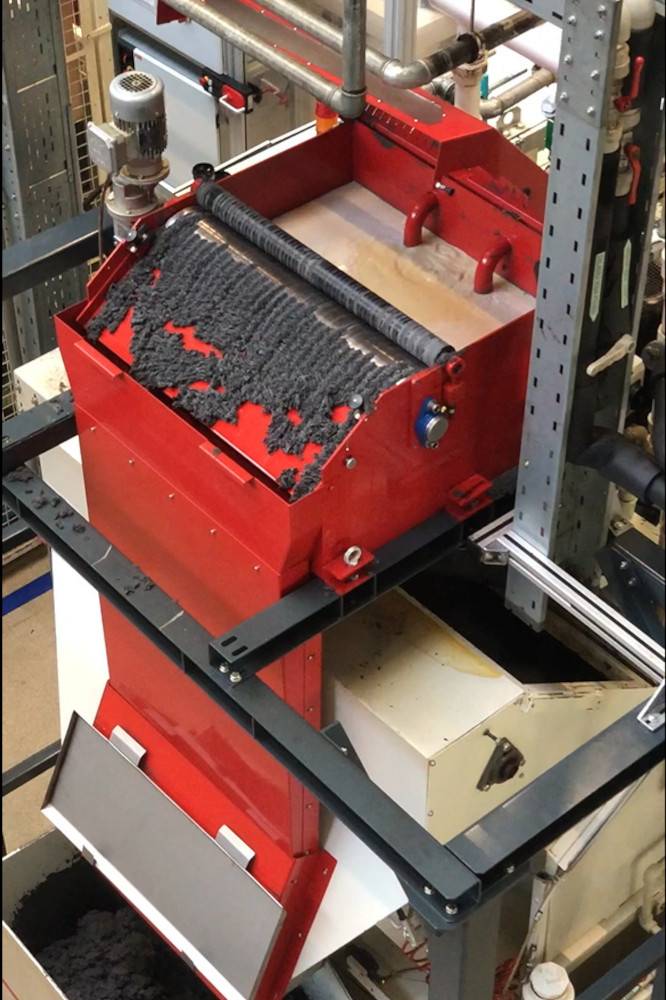
Return on investment within a few months
- Extension of coolant emulsion lifespan by 38 %
- Extension of internally cooled drill lifespan by 72 %
Initial situation
The customer specializes in honing and drilling using internally cooled drills. Maximum surface quality is essential in honing, making it necessary to keep the coolant emulsion absolutely clean. Ferromagnetic impurities contained in the emulsion shorten the lifespan of the drills and negatively impact the quality of the processed surfaces.
Problem description
Before installing the magnetic coolant separator, the cooling system would quickly clog and the internally cooled drills would wear out rapidly. The coolant emulsion was often contaminated with metal particles, leading to reduced machining quality and frequent emulsion replacement.
Solution
We designed and implemented a Magnetic coolant separator MVS-LUX 1000 N, equipped with a powerful magnetic drum containing the strongest neodymium magnets on the market. The unit, with a width of 1000 mm and a capacity of 480 litres of coolant per minute, was installed at a height of approximately 4 metres.
We engineered and manufactured the device including a supporting structure and contaminant discharge system, enabling the collected contaminants to be discharged directly into a collection container.
The equipment was fully installed and commissioned by our team.
Benefits of the MVS-LUX 1000 N
- Extension of coolant emulsion lifespan by 38 %
- Extension of internally cooled drill lifespan by 72 %
- Reduction in operating and maintenance costs
- Short return on investment – within a few months
MVS-LUX 1000 N – Advantages of the Device
- Continuous automatic operation – minimizes the need for manual intervention
- LUX separation cylinder – enhanced design for maximum separation efficiency
- Strongest neodymium magnets – ensure maximum capture of ferromagnetic particles
- High capacity – up to 480 l/min
- Robust industrial design – long service life and high durability
- Easy integration into existing production systems
Equipment used: Magnetic coolant separator MVS-LUX 1000 N